
More than 50 years of experience!
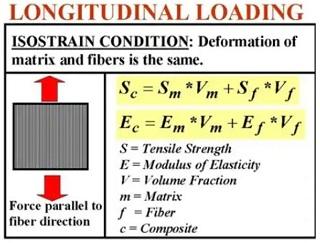
Already in the seventies, MeMC was investigating the mechancial behaviour of fibre reinforced composite materials. At that time, pioneers like Prof. Albert Cardon and Clem Hiel amongst others, performed experiments to validate the rule of mixtures. Although, the scientific community of composites was at that time still in its infancy, they mananged to estasblish long-standing relationships with renowned experts like - amonst others - W.T. Koiter & J.F. Besseling (UDelft), C.T. Heracovich, K. Reifsnider & Hall Brinson (Virginia Tech, US), S.S. Sternstein (Rensselaer Polytechnic Institute, US), S.A. Paipetis & G. Papanicolaou (UPatras, Greece), P. Hamelin, G. Verchery, A. Vautrin, Ayvaz Zaddeh (France), T. Marques (UPorto, Portugal), B. Adams (UBristol, UK) and K. Friedrichs (UKaiserslautern, Gemany).
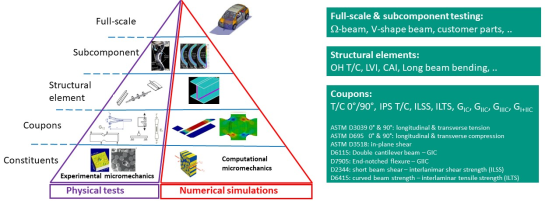
Today, capitalising on this long-standing experience and expertise and on the continuous investments in new technologies, we are capable of testing and characterising the mechanical performance of fibre reinforced composite material systems on all scales. Direct identification of intra-ply orientation dependent elastic and failure properties and of interlaminar strength and toughness and of intra-ply toughness can be performed following the ASTM-guidelines.
RECENT INVESTIGATIONS
Composite materials with different stacking sequences have been tested with Acoustic Emission in order to identify the occurring damage under multiaxial stresses. Optical microscopy has been used to monitor the damage during testing, whereas classification of the acoustic signals has allowed for the determination of the different damage types based on the multiaxial stress condition within the laminate.
![]() |
![]() |
Apart from small-scale testing, polymer composite components can be also tested. Indicatively, V-shape specimens and hollow beam components with a potential use in a composite vehicle frame for a suspension mount have been tested in our lab under dynamic loads. With the use of Digital Image Correlation and Acoustic emission, the distribution of damage throughout the components can be determined, as well as the different damage types occurring at various locations.
![]() |
![]() |
![]() |
![]() |
Current hot research topics are related to (i) the identification of interlaminar fracture properties, both in static and fatigue loading, in order to study crack nucleation and propagation under mode I, II, III and mixed mode loading and, (ii) the mechanical characterisation of thermoplastic composites in molten state.
![]() Mode I |
![]() Mode II |
![]() Mixed mode I&II |
Failure and fatigue under biaxial loading conditions
Around 1995, we started at MeMC to construct our home build biaxial test bench with a capacity of 100kN in both directions. Easier said than done, because it took us quite some years to get the system up and running and to design the proper specimen geometry.
Interesed readers are referred to the following papers for more detailed information:
- Design of a cruciform specimen for biaxial testing of fibre reinforced composite laminates (2006). Smits, A. ; Van Hemelrijck, D. ; Philippidis, T.P. ; Cardon, A. COMPOSITES SCIENCE AND TECHNOLOGY, Volume 66, Issue 7-8, Page 964-975. DOI10.1016/j.compscitech.2005.08.011
- Mixed numerical-experimental technique for orthotropic parameter identification using blaxial tensile tests on cruciform specimens (2007). Lecompte, D.; Smits, A.; Sol, H.; Vantomme, J.; Van Hemelrijck, D. INTERNATIONAL JOURNAL OF SOLIDS AND STRUCTURES, Volume 44, Issue 5. Page 1643-1656. DOI10.1016/j.ijsolstr.2006.06.050

Energy absorption under impact and blast loading
In the automotive industry, the plastic deformation capacity of steel is used for energy absorption of shock waves. However, it is a well-known fact that the specific energy absorption capacity of polymer matrix composites is much better than any conventional metal, if the composite structure is well designed]. The reason is their unique property for progressive failing under quasi-constant load. Therefore, it is not surprising that the automotive industry, but also the aerospace industry, investigate with great interest the opportunities of composite materials to improve the crashworthiness of primary structural components.
In civil engineering, the protection of critical infrastructure (tower buildings, embassies,...) against explosions has become an important research area. The objective of the studies performed, mostly in close collaboration with Prof. W. Van Paepegem (UGent), concerned the energy absorption capacity of composite structures that are capable of dissipating the energy of an explosion by stable and progressive failing and as such of protecting the critical structural members (columns, bridge pillars, walls,...) of civil engineering structures.
