
WHERE MATERIALS AND STRUCTURES MEET
Innovations in materials and structures have always been very closely related throughout history. As the most-used manmade material across the globe, concrete is everywhere, but this popular building material presents significant challenges related to its huge environmental impact and limited durability properties. The use of fibre textiles as reinforcement for concrete is one of the innovations that could provide a solution to the challenges that concrete structures are facing today.Textile reinforced concrete (TRC) can revolutionise the way concrete is being used as a construction material. In textile reinforced concrete, the traditional steel reinforcement is fully replaced by fibre textiles. The use of this innovative reinforcement has two important advantages: (i) the concrete cover, traditionally required to prevent the steel reinforcement from corroding, can be omitted and hence the thickness of concrete elements can be drastically reduced, and (ii) the flexibility of the fibre textile reinforcement allows to easily manufacture cutting-edge concrete structures with complex shapes.
Our research group focuses on developing novel structural concepts that benefit from this combination of high mechanical capacity, limited thickness, and fire safety of cement composites.
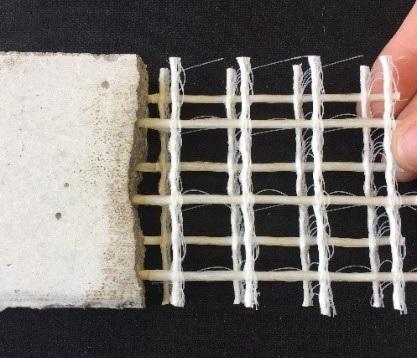
Currently investigated applications are loadbearing lightweight concrete structures such as sandwich panels and shells. One of the most promising applications of TRCs are indeed thin shells, as in these structures the benefits of the material can be fully exploited. The flexible reinforcement enables the design of extraordinary curved freeform shapes. Shells, when their shape is properly designed, are force-efficient structures experiencing mainly compressive forces. As a result, shells are intrinsically material efficient. Using TRC, ultra-thin shells of only a few centimetres thickness could be designed. Current ongoing research investigates the potential of modular precast shells to also make the manufacturing process more resource-efficient, and open reuse possibilities within a circular construction approach. Our research results show that design freedom is not at all compromised by modularity!
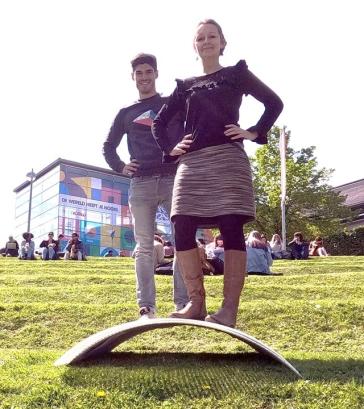
Another structural typology that fully benefits from the properties of TRC composites are insulating sandwich panels. When two cement composite skins are combined with a low-density, thermally insulating core, structural, lightweight and insulating sandwich panels with tremendous potential for the construction industry are obtained. These panels indeed tackle two sustainability issues at the same time! First of all, the thermal insulation of existing as well as novel buildings increases their energy efficiency and reduces the global energy consumption of the built environment. Secondly, the use of the structural sandwich concept with thin cement composite faces easily reduces the thickness, weight and material use of wall panels and systems.
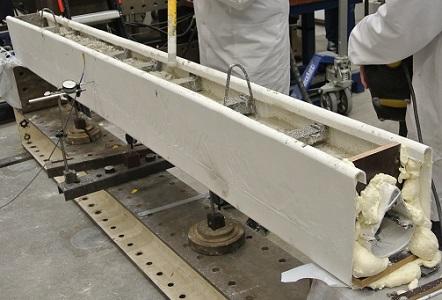
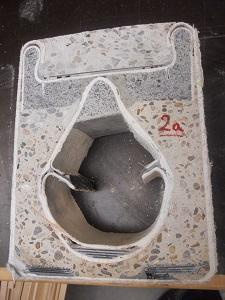
To facilitate the production of cement composite structures, we have performed pioneering work on the investigation of 3D textiles as reinforcement. 3D textiles (Figure 1a) are composed of two textile layers separated over a distance by means of knitted or woven connections. Thanks to this spaced geometry, the 3D textile acts as a rigid reinforcement during casting. On top of the clear manufacturing benefits compared to traditional 2D textile reinforcement, our research has demonstrated that 3D reinforced cement composites provide a superior flexural behavior due to the anchorage mechanism provided by the transversal connections. The 3D story continues as we are investigating the effects of adding also short fibres in addition to the 3D textiles to make an even more durable cement composite! Do keep track of our latest results in our ongoing FWO project Smart 3D-textile reinforced cementitious materials with microfibers, in collaboration with ULB colleague Prof. Didier Snoeck.
To enable the design of these fascinating cement composite structures, the research of our group includes research on both structural and material level. On structural level, we have expertise in the numerical and experimental analysis of these cement composite structures, their form finding and optimisation, and conceptual and structural design. On the material level, we work on the mechanical characterization, including durability studies and material modelling (analytical and finite element models). The picture at the right shows the 3D spacer textile developed specificaaly for this appication by 3D Weaving.
While cement composites are inherently firesafe compared to polymer-matrix composites, still the study of their behaviour under fire is essential. We work together with our colleagues from the University of Patras (Greece) on this topic.
Interested readers are referred to the following publications for more detailled description related to:
- new modelling approach for cement composites with spaced textiles: https://biblio.vub.ac.be/vubirfiles/75867081/A_layered_wise_Composite_M…
- To find out what happens if you put cement composite elements in a fire: https://www.mdpi.com/2076-3417/9/4/747

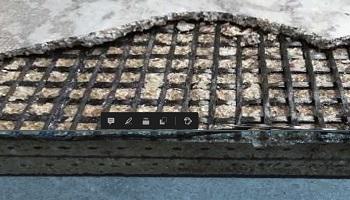