
ADDITIVE MANUFACTURING (AM)TOWARDS A HUMAN-CENTRIC, RESILIENT AND SUSTAINABLE FUTURE |
Industry 4.0 has seen the emergence of a number of technologies like amongst others Additive Manufacturing (3D printing) enabling faster, more flexible, and more efficient processes to produce higher-quality goods at reduced costs. Industry 5.0, the following significant and powerful industry shift emerging, provides a vison of industry that aims beyond efficiency and productivity as the sole goals, and reinforces the role and the contribution of industry to society. It places the wellbeing of the worker at the centre of the production process and uses new technologies to provide prosperity beyond jobs and growth while respecting the production limits of the planet.
The research activities of MeMC in the domain of additive manufacturing are focussing on the mechanical characterization of the materials and the processed structures. Two main material groups, polymers and metals, are studied.
![]() |
![]() |
3D-PRINTING OF FIBRE REINFORCED POLYMER
The environmental impact associated with the use of plastics has driven us to the study of a recycled alternative as feed for 3D printers. Together with polymer chemistry experts, we contribute to a reduction of the waste stream by developing filaments for fused filament fabrication (FFF), pellets for direct extrusion printing and powders for selective laser sintering, produced from recycled polyethylene terephthalate (PET). As 3D printed objects made from pure polymers lack in strength, prospects for enhancements in mechanical performance are explored by the incorporation of micro-reinforcing additives. Interested readers are referred to: B. Van de Voorde, et al., Effect of extrusion and fused filament fabrication processing parameters of recycled poly(ethylene terephthalate) on the crystallinity and mechanical properties, Additive Manufacturing, 50 (2022) 102518.
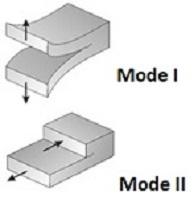
A critical failure mechanism in laminated fibre-reinforced polymer matrix composites is delamination. We study the fracture mechanics by testing (double cantilever beam (DCB), end notch flexure (ENF), end loaded split (ELS) and mixed mode bending (MMB) test) and simulation of mode I, mode II and mixed-mode delamination onset and growth in 3D printed composites.
Interested readers are referred to: E. Polyzos, A. Katalagarianakis, D. Van Hemelrijck, L. Pyl, 2021, Delamination analysis of 3D-printed nylon reinforced with continuous carbon fibers, Additive Manufacturing 46 (2021) 102144.
![]() |
![]() |
![]() |
![]() |
The widely used fibre-reinforced composites offer, in comparison to metals, lower weight and higher specific properties. In addition, 3D printed thermoplastic materials reinforced with long (continuous) fibres offer capability of custom reinforcement in specific areas and much more design freedom than conventional composites.
The 3D printing process, however, comes at the expense of a microstructure that is characterised by voids of various shapes, uneven distribution of fibres, uneven width of layers etc. We are currently focussing heavily on the experimental quantification of the geometric microstructural information and the elastic material properties and their influence on the macrostructural response. A generic approach should allow us to further build on this multi-scale framework for other material models and to study damage.
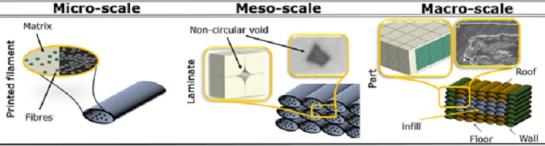
The overall goal of our team is to unravel 3D printed composites and to enhance the mechanical performance by tailoring the material and geometry to the needs in structural applications and with respect for the environment
Interested readers are referred to:
- L. Pyl, K.A. Kalteremidou, D.V. Hemelrijck, Exploration of the design freedom of 3D printed continuous fibre-reinforced polymers in open-hole tensile strength tests, Compos. Sci. Technol. 171 (2019) 135–151.
- E. Polyzos, A. Katalagarianakis, D. Polyzos, D. Van Hemelrijck, L. Pyl, A multi-scale analytical methodology for the prediction of mechanical properties of 3D-printed materials with continuous fibres, Additive Manufacturing 36 (2020) 101394.
3D-PRINTING OF METALS
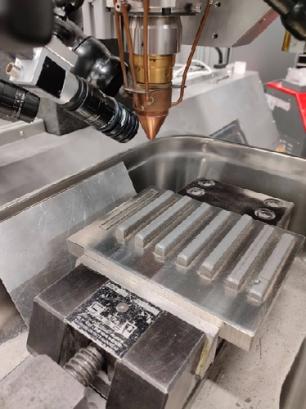
Our team is active in the analysis of the thermomechanical behaviour of 3D printed metals, and residual stresses in particular, in relation to the processing parameters. Residual stresses are detrimental to the performance of dynamically (i.e. fatigue) loaded parts as cracks might nucleate from surface areas with residual tensile stresses. Overcompensation for distortions leads to excessive milling and an increase in material waste. In that context, optical monitoring strategies and numerical models are combined to quantify residual stresses and distortions that develop in metal parts (for example 316L stainless steel), additively manufactured with the laser metal deposition technique (LMD). Thanks to the full control over the process with the in-house build LMD platform and possibility to introduce inline monitoring strategies, and to the extensive set of mechanical test facilities and monitoring equipment, we perform inline and ex-situ tests to better understand the material and process and to attain parts with an improved quality and mechanical performance. Expertise and methods from different disciplines (metallurgy, surface engineering and mechanical engineering) are brought together to study the influence of processing conditions and post-treatments on the mechanical (fatigue) performance and damage initiation.